Zweifellos enthält die Alchemie einen Abschnitt, welcher der Erschaffung von Megalithen gewidmet ist, aber der „Stein der Weisen“ ist nicht der Hauptgegenstand dieser Wissenschaft.
Diese ist so vielseitig und tiefgehend, daß alle modernen Kenntnisse aus Physik, Chemie, Astronomie, Geologie und Anthropologie auch nicht ein Zehntel davon enthalten, womit sich die Alchemie befaßt.
Ich spreche von ihr in der Gegenwart, weil ich davon überzeugt bin, daß sie auch heute nirgendwohin verschwunden ist. Sie entwickelt sich auf ihre Weise, ohne ihre Tätigkeit an die große Glocke zu hängen.
Nur manchmal kommen einzelne Teile von ihr ans Licht – solche, wie zum Beispiel die DNS-Genealogie, und die Gen-Ingenieurtechnik, einschließlich der Klon-Technologie.
Wofür hat man dir das angetan, Megalith?
Aber ungeachtet des Weggangs der Alchemie in den Untergrund waren ihre Geheimnisse noch eine hinreichend lange Zeit zugänglich. Zum Beispiel kam noch im Jahre 1931 ein sehr rätselhaftes Buch in Leningrad heraus, das eine Umwälzung in der Welt der Wissenschaft vollziehen sollte.
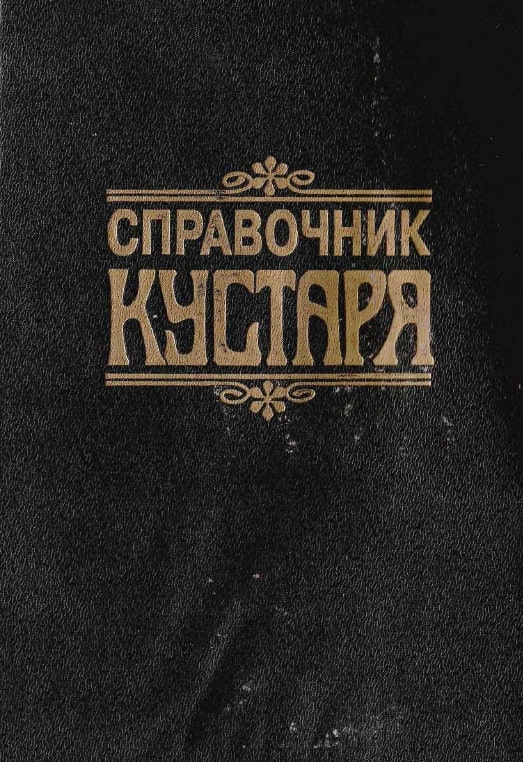

Sollte, hat aber nicht ..
Schaut selbst. Hier ist einer der Abschnitte dieses Buchs, das der Erschaffung der „Steine der Weisen“ unterschiedlicher Art gewidmet ist:
I. Künstlicher Marmor und Granit
- Künstlicher Marmor nach Borchardt
1.1. Die Masse wird aus reinem Quartzsand, kohlensaurem Kalk, Talkum und Gips zubereitet, zu denen noch ein wenig feingemahlener Farbstoff hinzugefügt werden kann. Der verwendete Sand muß aus reiner Kieselerde bestehen, und für diesen Zweck wird er gewaschen und von allen organischen Bestandteilen gereinigt. Nach der vollständigen Durchtrocknung des Sandes werden 5 – 6% Trepel (ein poröses leichtes Mineral, das aus Kieselerde und Tonerde besteht – d.Ü.) zugesetzt. Danach wird als Bindemittel auf jeweils 100 Teile Sand 6 – 7 Teile kohlensaurer Kalk zugesetzt, sowie 3 Teile Talkum, 4 Teile Gips und 3 Teile Feldspat.
Alle genannten Bestandteile werden mit einer geringen Menge Wasser vermischt. Die erhaltene Masse wird in eine Form eingebracht und nach ihrer vollständigen Durchtrocknung bei weißglühender Hitze in einem Ofen ohne Luftzug gebrannt.
1.2. Es werden 80 Teile Gips und 20 Teile kohlensaurer Kalk kleingerieben, gemischt und mit einem Gemisch von 1000 Teilen destilliertem Wasser und 1080 Teilen schwefelsaurem Kalk vermischt.
1.3. Man nimmt 1000 Teile Wasser, 1440 Teile Klebstoff und 1000 Teile Schwefelsäure. Dann wird der Teig daraus in eine Form gelegt und wenn er hart geworden ist, entnimmt man ihn, trocknet ihn zwei Stunden, schleift und poliert ihn in üblicher Weise.
Schließlich wird das Teil in eine Wanne aus Leinöl bei 70° Wärme getaucht, hernach getrocknet und mit Stearin eingerieben. Zur Färbung werden Anilinfarben empfohlen.
1.4. Künstlicher Marmor blaß-gelb bis weiß. 30 Teile grober weißer Sand, 42 Teile Kreide, 24 Teile Kolophonium und 4 Teile Branntkalk.
1.5. Grünlicher. 28 Teile grober Sand, 42 Teile Kreide, 2 Teile blauer Ultramarin, 24 Teile Kolophonium und 4 Teile Branntkalk.
1.6. Körperfarben. 28 Teile grober Sand, 42 Teile Kreide, 1 Teil blauer Ultramarin, 1 Teil Zinnoberrot, 24 Teile Kolophonium, 4 Teile Branntkalk.
- Marmor-Imitation
2.1. Nach Van-der-Stien.
Zuerst bereitet man Wasser vor, in welches der Gips eingerührt werden muß, ergänzt dazu Tischlerleim und Harz; der Leim wird in üblicher Weise in warmem Wasser gelöst, das Harz in einem warmen Terpentin-Bad.
In das auf diese Weise vorbereitete Wasser wird Gips so eingerührt, daß die ganze Masse für das Ausfüllen der Form reicht. Danach werden in das Gemisch die für die Färbung des Marmors notwendigen Farben ergänzt; die Farben sind in speziellen Gefäßen vorzubereiten.
Der auf diese Weise vorbereitete und gefärbte Marmor wird dann in eine Form aus Gips, Zement oder Kautschuk gegossen, für ebene Platten auf gläserne oder steinerne Tafeln.
Diese Marmorschicht wird in einer Dicke von 4 mm aufgebracht, danach wird eine Schicht trockener Gips draufgesiebt, um das überschüssige Wasser zu entfernen, das für das Lösen des gefärbten Gipses benutzt worden war.
Sobald diese Schicht pulverförmiger Gips sich gut mit dem Wasser, das im gefärbten Gips enthalten ist, durchfeuchtet hat, wird darauf eine dünne Schicht gut gelösten Gipses gegossen, und darauf wird Leinen oder Tuch gelegt.
Sodann folgt eine Schicht gelöster Gips, dem zerkleinerter Schotter beigemengt wurde. Diese letzte Schicht hängt von der Dicke ab, welche man dem Gegenstand geben will, der aus dem künstlichen Marmor herzustellen ist.
Sobald die Masse ausreichend fest geworden ist (im Verlaufe von 6 – 8 Stunden), wird sie von der Platte oder aus der Form genommen, mit Bimsstein abgerieben und die in der Masse vorhandenen Poren werden mit gelöstem Gips, der in der Hauptfarbe des gegossenen Gegenstandes gefärbt ist, gefüllt.
Um die Oberfläche wasserundurchlässig zu machen, wird sie mit siliziumsaurem Kalium bearbeitet, indem man sie entweder in eine Wanne taucht oder die Flüssigkeit mit Hilfe eine Pinsels aufbringt.
Wenn die Masse vollständig getrocknet ist, wird die Oberfläche poliert, wobei die Neuheit des Polierprozesses darin besteht, daß mit einem Tampon poliert wird, der mit einem Lappen umwickelt ist, welcher mit der nach einem besonderen Rezept gefertigten Politur getränkt ist:
2.1.1. Weiße Politur für hellen künstlichen Marmor: 100 Teile geweißten Gummilack, 600 Teile Alkohol, 25 Teile feingemahlener Gips.
2.1.2. Braune Politur: 100 Teile Gummilack orangener Farbe, 600 Teile Alkohol, 25 Teile feingemahlener Gips.
Zuerst wird der zu polierende Gegenstand mit einem in Alkohol getränkten Tampon abgerieben, dann wird die Politur mit einem anderen Tampon aufgetragen und mit diesem Tampon solange verrieben, bis ein gewisses Anhaften zu bemerken ist.
Die auf diese Weise hergestellte Politurschicht wird mit dem ersten mit Alkohol getränkten Tampon nachgearbeitet, bis eine vollständig glatte Oberfläche entsteht.
2.1.3. Schwarze Politur: hierfür wird auf einen Lappen ein wenig schwarze Anilinfarbe gegeben. Um eine gleichmäßige und sehr glänzende Politur zu erreichen, ist es notwendig, einen den Tampon überdeckenden Lappen von Zeit zu Zeit mit einigen Tropfen Öl zu schmieren.
2.2. Nach Rosmer.
Die aus gewöhnlichem Kalk hergestellten Gegenstände – Vasen, Figuren usw. – werden im Verlaufe von 12 Stunden bei einem Druck von 5 Atmosphären mit kochendem Wasser oder Dampf erwärmt.
Danach werden sie in eine Wanne gegeben, die aus einer Lösung von Alaun bei 5° nach B. besteht, in welcher sie von einem Tag bis zu mehreren Wochen verbleiben.
Auf diese Weise erhält der Stein eine höhere Härte und die Fähigkeit, eine Politur anzunehmen.Wenn man den Stein färben will, dann gibt man der Masse in Wasser gelöste Anilinfarben bei.
2.3. Nach Ostermeier.
Man mischt Kalkmilch mit fein zerstoßenem Marmor oder Kalkmilch mit Kreide, und zwar solange, bis eine Art dünner Brei entsteht.
Auf der Grundlage der Untersuchungen des Pompeji-Zements empfiehlt Ostermeier, zu diesen Masse eine hinreichende Menge grob zerstoßener Kalksteine hinzuzufügen. Dieser Zement trocknet und härtet sehr bald.
- Granit-Imitation
Es wird reiner feiner Sand mit Kies oder einer anderen Masse, welche Kieselstein enthält, gemischt, auch mit frisch gebranntem und zerkleinertem Kalk in folgenden Proportionen: 10 Teile Sand oder Kies und ein Teil Kalk. Der Kalk wird durch die Feuchtigkeit des Sandes gelöscht, zersetzt den Kiesel und bildet eine dünne Schicht um jedes Silizium-Sandkörnchen. Beim Erkalten wird das Gemisch mit Wasser erweicht. Dann werden 10 Teile zerstoßener Granit und ein Teil Kalk getrennt gemischt.
Beide Gemische werden dergestalt in metallische Formen getan, daß das Gemisch von Sand und Kalk die Mitte des Gegenstandes bildet und das Granit-Gemisch mit Kalk die äußere Hülle von 6 bis 12 mm Dicke (je nach Dicke des herzustellenden Gegenstandes).
Abschließend wird die Masse gepreßt und erhält durch das Trocknen an Luft ihre Härte.
Als Färbemittel dienen Eisenerz und Eisenoxid, welche heiß mit dem körnigen Granit vermischt werden.
Wenn man Gegenstände, die aus dem obengenannten Gemisch geformt werden, eine besondere Härte geben will, so lege man sie für eine Stunde in siliziumsaures Kalium und erhitze sie auf 150 °C.
II. Verschiedene künstliche Massen
Für die Zubereitung dieser Masse wird Magnesit zerkleinert und in faustgroßen Stücken in Retortenöfen, welche in Gaswerken benutzt werden, gebrannt. Das Eisenmagnesit wird in Kollermühlen zerkleinert, durch ein Haarsieb durchgesiebt und dabei mit einer entsprechenden Menge Trepel vermischt.
Aus diesem Zementpulver, in Wasser gelöst, kann man Ornamente ausarbeiten, wie aus Gips, aber mit Gips kann dieses nicht konkurrieren. Jedoch hat es eine andere wertvolle Eigenschaft, und zwar gibt es im Verbund mit einer mäßig starken Lösung Chlor-Magnesium eine harte und plastische Masse.
Eine in der richtigen Proportion angemischte Albolit-Zementmasse sollte, je nach Verwendungszweck, die Konsistenz eines mehr oder weniger zähen dünnen Breis aufweisen, welcher unter dem Einfluß der Arbeitstemperatur langsam eindickt und nach 6 Stunden aushärtet.
Wenn die Masse soweit hart geworden ist, daß man auf ihr die Fingernagelspuren sieht, wird in ihr ein Prozeß der Selbstverwärmung vor sich gehen, der in Abhängigkeit von der Größe und der Dicke des herzustellenden Gegenstandes unterschiedlich ist; dicke Platten erhitzen sich zum Beispiel auf über 100 °C.
Beim Gießen großer Gegenstände ist das ein schwer zu verhindernder Mangel und Klebeformen kann man nur mit großer Vorsicht anwenden. Man muß den Gegenstand früher aus der Klebeform herausnehmen, bevor der Erwärmungsprozeß beginnt.
Beim Gießen von kleinen Gegenständen ist die Erwärmung unbedeutend und stellt daher kein Hindernis dar. Die Plastizität der Masse ist außergewöhnlich groß.
Für Gipsornamente hat die Albolit-Masse den Vorteil, daß wenn man das Gipsornament mit einer dünnen Schicht Albolit überzieht, und dies wiederholt solange, bis nichts mehr eingezogen wird, dann erhält das Ornament äußerlich eine höhere Festigkeit.
Aus dieselbe Weise kann man auch anderen Materialien eine höhere Festigkeit verleihen. Für das Reparieren von Sandstein gibt es kein geeigneteres Material als den Albolit-Zement.
Mehrjährige Versuche haben gezeigt, daß es praktisch ist, Häuser mit Albolit zu schmieren. Im Haus ist es sehr praktisch, Treppenstufen, Böden usw. damit zu schmieren.
Holztreppen, die sich außerhalb befinden, wird empfohlen, mit einer Schicht Albolit zu überziehen.
Beyerit st ein Skulptur-Material, das vom Skulptor Beyer in Paris erfunden wurde – es ist für kleinste Güsse geeignet wie auch für die größten Abmessungen, es übermittelt Konturen und Linien mit einer solchen Präzision, die man mit Gips niemals erreichen kann. Die Oberfläche der Gußteile, die man auch polieren kann, ist reinweiß und weist fast den gleichen Glanz und die gleichen Reflexe auf wie natürlicher Marmor.
Besonder gut ist diese Masse geeignet für das Gießen von Statuen – sie verleiht wie auch der Marmor diesen den Eindruck von Weichheit und Belebtheit, dank dem Spiel von Licht und Schatten.
An den Bruchstellen hat Beyerit einen kristallischen Aufbau, der sich durch eine ausreichend große Härte auszeichnet. Die gegossene Masse härtet schon nach einer Stunde aus und erfordert nur in seltenen Fällen noch eine nachfolgende Bearbeitung. Beyerit besteht aus 100 Teilen Marmorstaub, 10 – 25 Teilen Glaspulver, 5 – 10 Teilen in Pulver verwandelter gesiebter Kalk, gelöst im Wasserglas.
- Marmorit
Nach Losse wird dieses aus gleichen Teilen kleingemahlenem, geschlämmtem und geglühtem Magnesit und einer Lösung von schwefelsaurem Magnesium hergestellt. Beide Teile werden gut miteinander vermischt und das Gemisch wird in eine mit Fett geschmierte Form gegossen. Nach dem Festwerden der Masse kann man diese mit warmem Seifenwasser auswaschen.
Die festgewordene Masse sieht aus wie weißer Marmor und mit der Zeit gewinnt sie auch dessen Härte, so daß man sie zum Gießen von Büsten, Statuen usw. verwenden kann. Dabei kann man dieselben Formen verwenden, wie sie für Gipsarbeiten benutzt werden.
III. Harte Gipsmassen
- Kalkiger Gips
Um dem Gips mit Hilfe von Kalk mehr Härte zu verleihen, löscht man fetten Kalk vorsichtig ab, so daß er zu einem feinen Pulver zerfällt, und mischt das gewonnene Pulver in einer Menge von 10 Gewichts% des Gips mit letzterem. Zum Erhalt eines homogenen Gemisches werden die Pulver nach Möglichkeit in einem rotierenden Faß gemischt, damit eine ungleichmäßige Verteilung in der Masse nicht zu Unebenheiten in der vergossenen Masse führt.
Kalkiger Gips muß sorgfältig vor dem Zutritt von Luft bewahrt werden, damit der Kalk nicht das Kohlendioxyd anziehen kann. Die aus kalkigem Gips gegossenen Gegenstände werden nach einigen Monaten durch das Anziehen vom Kohlensäure-Anhydrid aus der Luft härter als solche aus gewöhnlichem Gips gegossene.
- Alaun-Gips
Für die Herstellung von Alaun-Gips wird Alabaster kleingemahlen und in einem rotierenden Faß sorgfältig mit 1/12 seines Gewichtes von zu feinstem Pulver zerstoßenem Alaun vermischt. Das Gemisch wird wird dann in kleinen Pfannen leicht gebrannt, wodurch eine leicht gelbliche Masse entsteht, die man leicht zu Pulver verarbeiten kann.
Beim Zerreiben des Alaun-Gipses mit Wasser entsteht eine dünnflüssige Masse, die erst nach 40 – 60 Minuten fest wird. Eine wenig gebrannte Masse verfestigt sich schneller als eine stärker durchgebrannte.
Eine gute Alaun-Gips-Masse kann man auch aus gewöhnlichem gebranntem Gips herstellen, wenn man anstelle von einfachem Wasser solches Wasser verwendet, in dem zu gleichen Teilen Alaun und Salmiak gelöst sind.
- Schwefelsaures-Kalium-Gips
Kann man nur zubereiten aus Gips, der frei ist von Kohlensäure-Kalk. Um diesen davon zu befreien, wird beim Mischen der Gipsmasse mit dem schwefelsauren Kalium kein reines Wasser verwendet, sondern mit Schwefelsäure angesäuertes.
Das feine Pulver von schwefelsaurem Kalium und das Gipspulver werden, wie auch beim kalkigen Gips, in einem rotierenden Faß gemischt.
Aus Schwefelsaures-Kalium-Gips gegossene Gegenstände sind leicht durchscheinend und zeichnen sich durch einen besonderen Glanz aus.
- Zink-Vitriol-Gips
Wird folgendermaßen gewonnen: in Wasser, das für das Zerreiben des Gips benutzt wird, löst man schwefelsaures Zink (Zink-Vitriol) und mit dieser Lösung wird der Gips bearbeitet.
- Borax-Gips-Masse
Wird wie folgt erhalten: zuerst wird eine kalte gesättigte Borax-Lösung zubereitet, indem man in kochendem Wasser so viel Borax löst, wie sich lösen kann. Dann läßt man diese Lösung 48 Stunden stehen und gießt die Lösung vom kristallisierten Borax ab.
In diese Lösung werden gebrannte Gipsstücke getan, den ganzen Tag darin belassen und nach dem Trocknen erneut gebrannt. Dabei wird bis zur rotglühenden Hitze erhitzt, um aus dem Borax das ganze Kristallwasser auszutreiben.
Danach werden die Gipsstücke gemahlen und mit Wasser zerrieben, in dem auf 100 Teile Wasser 10 Teile kohlensaures Natrium oder Kalium gelöst sind, und dann in die Form gegossen.
Die Borax-Gips-Masse härtet sehr langsam aus, weist aber nach einiger Zeit soviel Härte auf, daß man sie schleifen und polieren kann, wie natürlichen Kalkstein.
- Harte Gipsmasse nach Juhle
6 Teile Gips werden mit 1 Teil feingesiebtem frisch abgelöschtem Kalk vermischt und dieses Gemisch wird wie gewöhnlicher Gips verarbeitet. Danach, wenn diese Masse gut austrocknet, werden die fertigen Gegenstände mit einer Lösung von Eisen- oder Kupfer-Vitriol getränkt, dessen Basis sich mit Kalk absetzt und einen nicht löslichen Niederschlag ergibt.
Der zwischen den Gipsporen enthaltene Kalk zerlegt das Kupfervitriol und bildet zwei nicht lösliche Stoffe, und zwar: Schwefel-Kalzium-Salz und metallische Oxyde, welche die Poren des Gegenstandes vollständig ausfüllen.
Bei Verwendung von Zinkvitriol bleibt die Masse weiß. Bei Eisenvitriol wird sie anfangs grünlich gefärbt, aber beim Trocknen erhält sie die für Eisenoxyd charakteristische Färbung. Mit Eisen entsteht die härteste Masse; ihre Widerstandsfähigkeit ist um 20mal höher als die von gewöhnlichem Gips.
Um ein Maximum an Härte und Festigkeit zu erzielen, muß man möglichst schnell das Kalk-Gips-Gemisch mit der erforderlichen Menge Wasser vermischen. Vor dem Abhärten mit Vitriol muß die Masse gut getrocknet werden, damit die Lösung sie leicht durchtränken kann. Die Lösung muß gesättigt sein und der Gegenstand darf nicht länger als zwei Stunden darin eingetaucht werden.
Auf dem dieserart hergestellten Gips darf man keine Fingernagelkratzer mehr machen können. Wenn zu lange in die Lösung getaucht wurde, dann wird der Gips brüchig; wenn er nach dem ersten Eintauchen ausgetrocknet ist, dann wird ihm ein Zusammentreffen mit Wasser keinen Schaden zufügen.
Wenn man zuviel Kalk zusetzt, dann geschieht es, daß die Oberfläche so fest wird, daß sie kein Wasser und kein Öl aufnimmt. Die Oberfläche wird tatsächlich so hart, daß man sie mit einem Glas-Schmirgelleinen wie Marmor schleifen kann, der Nachteil ist, daß die harte Schicht nicht dicker als 2 mm ist, wodurch die Masse keinen ausreichend hohen Widerstand gegen Zusammendrücken aufweist.
Die Proportionen von Kalk und Gips können in weiten Grenzen variiert werden, aber Juhle hat die besten Ergebnisse mit einem Verhältnis von 1:6 erzielt. Die mit Eisenvitriol gehärteten Gipsgegenstände weisen eine rostig-braune Färbung auf, aber wenn sie mit gekochtem Leinöl getränkt werden, das vom Erhitzen braun geworden ist, dann bekommen sie die Färbung von Mahagoni. Wenn man sie dann noch mit einem Kopallack überzieht, dann erhalten sie ein sehr schönes Aussehen.
- Harte Gipsmasse nach Heynemann
Die nach diesem Verfahren aus rohem Gipsstein hergestellten Gegenstände werden zuerst auf 100 – 120 °C erhitzt, zum Entfernen eines Teiles ihres Kristallwassers. Hernach werden die Gegenstände in eine konzentrierte Lösung von chlorigem Kalzium gelegt und nach deren Sättigung in eine heiße konzentrierte Lösung von schwefelsaurem Magnesium. Dadurch setzt sich im Gips das Schwefel-Kalzium-Salz ab, welches das beim ersten Erhitzen entfernte Kristallwasser ersetzt, und die Gegenstände werden fester, mit höherer Widerstandsfähigkeit, wobei sich das gebildete chlorige Magnesium beim Eintauchen der Gegenstände in Wasser herauslöst.
Nach dieser Bearbeitung erfolgt ein zweites Erhitzen, Sättigen in einer Lösung chlorigen Kalziums und Absetzen mit Hilfe des schwefelsauren Magnesiums.
Diese Bearbeitung kann man noch einige Male wiederholen. Bei solchem erneutem Erhitzen kann man die Temperatur soweit erhöhen, daß sie schließlich bis zu 400°C erreicht.
Nachdem man die Gegenstände mit dem obengenannten Verfahren durchtränkt hat, werden sie abwechselnd mit Kleber- und Tannin-Lösung, jedes Mal von 1 bis 4 Tagen je nach den Abmessungen der Gegenstände, bearbeitet und anschließend in einem Trockner bei stetig abnehmender Wärme getrocknet.
Anstelle von Tischler-Leim kann man solche Stoffe benutzen, die mit entwässertem Schwefel-Kalzium-Salz in Wasser unlösliche Verbindungen ergeben, zum Beispiel Blutserum, Gluten in flüssiger Form, austrocknende Öle und ähnliches.
Genauso kann man die Verbindung des Klebers mit dem Schwefel-Kalzium-Salz durch eine Alaun-Lösung hervorrufen.
Für die Herstellung von farbigem Marmor vermischt man eine Lösung von chlorigem Kalzium mit solchen Metall-Chloriden, die bei anschließender Bearbeitung mit metallischen Salzen farbige, nicht lösliche Niederschläge bilden, anstelle des ausgetriebenen Kristallwassers.
Wenn zum Beispiel die Lösung des chlorigen Kalziums mit Chlor-Eisen verbunden wurde, so erhält man bei Bearbeitung mit chromsaurem Kalium einen braunen unlöslichen Niederschlag von chromsaurem Eisen bei der Bildung und Ablagerung des chromigen Kaliums. Die weitere Bearbeitung ist ähnlich dem oben beschriebenen.
- Harte Gipsmasse nach Denstädt
Eine heiße gesättigte Barium-Lösung wurde bisher nicht empfohlen zum Härten von Gipsgüssen; aber bei Beachtung der bekannten Vorsichts-Maßnahmen kann eine Barium-Lösung verwendet werden und gibt sehr befriedigende Ergebnisse.
Beim Verwenden dieser Lösung ist vor allem die Herausbildung von Barium-Kristallen während des Aufbringungs dieser Lösung zu verhindern. Dies erreicht man dadurch, daß die Gegenstände vor dem Durchtränken auf 60 – 80°C erwärmt werden.
Damit wird gleichzeitig erreicht, daß die aufgebrachte Lösung durch den Außendruck der Luft in eine bedeutende Tiefe reingedrückt wird. Beim Abkühlen werden die Barium-Kristalle sich erst innerhalb der Masse bilden und beim Durchtrocknen nicht an die Oberfläche kommen, sondern verbleiben drinnen und bilden unlösliche Verbindungen.
Eine weitere Schwierigkeit besteht darin, daß zum Aufbringen der Lösung die gewöhnlichen Pinsel oder Schwämme nicht verwendet werden können, da sie augenblicklich durch die ätzende Flüssigkeit zersetzt werden.
Daher werden Pinsel mit Glasfäden eingesetzt. Diese stellt man her, indem man die Fäden in Glasröhrchen einklebt, mit einem Kleber, der aus Wasserglas und Muschelschalen besteht. Eine Reihe dünner Pinsel wird in einem breiten Glasrohr vereint und mit demselben Kleber verklebt.
Zum Erreichen einer höheren Härte werden dem Gips entweder freie Silizium-Säure oder metallische Salze beigemengt, welche mit Barium eine solche Reaktion eingehen, so daß neben dem unlöslichen Barium-Salz nicht lösliche Metalloxyde oder Hydrate der Oxyde entstehen.
Bei Verwendung freier Silizium-Säure wird diese in staubfeinem Zustand dem Gips vor dem Formen beigemengt. Man kann deren Menge um 50% erhöhen, ohne beim Gips die Fähigkeit zum Festwerden zu verringern. Gegossene und getrocknete Gegenstände werden auf 60 – 70 °C erwärmt und mit der heißen Barium-Lösung getränkt.
Anstelle der freien Silizium-Lösung kann man auch den in der Porzellan-Produktion verwendeten Glasursand nehmen, der aus der Umwandlung von gebranntem Quarz in Pulver erhalten wird.
Unter dem Einfluß der atmosphärischen Kohlensäure verbindet sich das Barium mit dem Kohlensäure-Hydrat zu einer festen Masse, ähnlich wie Kalk sich mit Sand verbindet.
Die oben angeführten metallischen Salze sind vor allem metallische Sulfate (Zink, Cadmium, Magnesium, Kupfer, Eisen, Aluminium, Chrom, Kobalt, Nickel).
Gips löst sich mit diesen Salzen oder die gegossenen Gegenstände werden mit Lösungen dieser Salze getränkt. Nachdem man sie vorsichtig ausgetrocknet hat, werden sie auf 60 – 70 °C erwärmt und mit der heißen Barium-Lösung bearbeitet.
Einige der obengenannten Salze rufen gleichzeitig auch eine Färbung der Gegenstände hervor. Man kann eine völlig gleichmäßige Färbung erreichen, wenn man anstelle des Barium-Hydrates Kalk verwendet. In diesem Falle ist der Bearbeitungsprozeß ein umgekehrter. Zum Gips wird vor dem Lösen der Branntkalk zugesetzt (bis zu 5%) oder noch besser wird der Gips in Kalkmilch gelöst und die gegossenen Gegenstände werden nach dem Trocknen mit den Lösungen der obengenannten Salze durchtränkt.
- Harte Gipsmasse nach Keeting
Gips erhält eine höhere Härte und Festigkeit, wenn er in eine Borax-Lösung gelegt wird. Dazu werden 5 Teile Borax in 45 Teilen Wasser gelöst, in diese Lösung legt man die Gipsstücke derart, daß sie davon vollständig bedeckt sind, und läßt sie darin solange, bis sie sich vollständig mit der Lösung durchtränkt haben, wonach man sie einer starken Erhitzung im Verlaufe von 6 Stunden zuführt und nach dem Abkühlen zu Pulver verwandelt.
Noch bessere Härte erhält man, wenn mit Hilfe von Erwärmung 4 Teile Weinstein und 4 Teile Borax in 72 Teilen Wasser löst. Nach der Auflösung geht man wie oben beschrieben vor.
- Harte Gipsmasse nach Winkler
Gips (Alabaster) wird getrocknet, indem man ihn gewöhnlicher Hitze im russischen Ofen aussetzt, wie man sie zum Backen von Brot benötigt; dabei sind für ein Stück, dessen Dicke 30 cm nicht überschreitet, 3 Stunden ausreichend; nach deren Ablauf wird es abgekühlt, in Wasser innerhalb von 30 Sekunden angefeuchtet, für einige Sekunden der Luft überlassen und nochmals für 2 Minuten in Wasser befeuchtet.
Anschließend wird es für einige Tage an der Luft stehengelassen, wovon der Gips hart wird wie Marmor.
IV. Imitationen von Bausteinen
- Künstlicher Stein
1.1. 2 Teile hydraulischer Kalk, vermischt mit einer Alaun-Lösung in der 15fachen Wassermenge, 10 Teile Sand und 1 Teil Zement werden zu einer Masse vermischt, welche man in Formen preßt und nach 24 Stunden herausnimmt. Die Steine sind nach 14 Tagen zur Verwendung bereit, werden aber erst im Verlaufe der Zeit richtig hart.
1.2. Ein Gemisch aus 1 Teil Zement und 3 Teilen Sand wird in verdünnter Schwefelsäure (100 Teile Wasser auf 2 Teile Säure) gelöst und unter starkem Druck gepreßt. Die Steine werden im Verlaufe von zwei Tagen an der Luft getrocknet, für 12 Stunden in verdünnte Schwefelsäure (2 Teile Säure auf 100 Teile Wasser) gelegt und erneut getrocknet.
1.3. 2 Teile Portland-Zement, 1 Teil Sand und 1 Teil Schlacke werden in trockenem Zustand vermischt und dann mit einer wäßrigen Lösung von Eisenvitriol befeuchtet. Die dickflüssige Lösung wird in Formen gepreßt, mehrere Wochen getrocknet: 2 an einem warmen Ort, dann für 24 Stunden in Wasser gelegt und schließlich 4 Wochen getrocknet.
1.4. 10 Teile ungelöschter Kalk werden sorgfältig mit 3 – 4 Teilen Wasser vermischt, dann werden 40 – 60 Teile trockener Sand zugesetzt und 2,5 – 10 Teile hydraulischer Zement, und das Ganze wird nochmals gut durchgemahlen. Dann wird die Masse in Formen gepreßt.
1.5. 1 Teil ausgelaugte Asche, 1 Teil Harz, 1/8 – ¼ Teil Leinöl werden unter ständigem Umrühren in einem Kessel erhitzt und in Formen gegossen.
1.6. 15 l Klebstoff-Wasser, ¼ l Wasser, in welchem Tischlerleim gelöst wurde, und 1/8 kg Borax-Pulver werden mit einer solchen Menge Gips vermischt, daß sich eine teigartige Masse ergibt, die zum Pressen geeignet ist. Durch Zusatz von Farstoffen erhält man eine farbige Masse.
1.7. 200 kg Sand oder Schotter, 75 kg Harz und 20 l Holzteer werden mit einer ausreichenden Menge zerstoßener Steine vermischt und, je nach Farbwunsch, werden venezianische Farben oder Gips hinzugefügt und das Ganze stark erhitzt.
1.8. 4 Teile Kies und ein Teil Zement werden – je nach Wunsch unter Hinzufügung von Schotter u.ä. – mit Wasser verrührt. Die Masse wird in Formen getan, wo auf deren Oberfläche eine Schicht von etwa ½ cm Dicke getan wird, die aus 1 Teilen feinem Sand, 1 Teil Zement und 1 Teil trockner Mineralfarbe als Pulver besteht. Wenn man die Steine an der Oberfläche mit einem Muster versehen will, dann wird dieses auf den Boden getan und darauf die genannte Farbschicht. Wenn der Stein fast trocken ist, wird seine Oberfläche mit verdünntem Wasserglas bestrichen. (mit solche Platten sind einige Straßen in New York gepflastert).
1.9. 30 Teile Quarzsand und 1 Teil Bleioxyd werden mit 10 Teilen Wasserglas vermischt und, wenn nötig, mit entsprechenden Farbstoffen, in Formen gepreßt und dann im Verlaufe von 2 Stunden rotglühend gemacht.
1.10. Hydraulischer Kalk wird in einen etwa 1/8 Tonnen fassenden Korb gelegt und in ein Gefäß mit Wasser getaucht, in dem er solange verbleibt, bis keine Luftblasen mehr aufsteigen. Dann den Korb aus dem Wasser heben, abtropfen lassen und mit einem umgedrehtem Eisenkessel überstülpen. Die Ränder des Kessels, der auf dem Boden steht, werden rundum mit Asche bestreut, so daß es keinen Luftaustausch mit unter dem Kessel gibt.
Den Kalk läßt man 12 Stunden so stehen, nach deren Ablauf er sich in feines Pulver verwandelt. Dieses Pulver verwendet man für die Steinherstellung.
1 Teil dieses Kalks mischt man mit Wasser so, daß eine flüssige Grütze entsteht, und dann fügt man 2 1/2 Teile Schiotter und ½ Teil Steinkohlen-Asche, Torf oder ausgelaugte Holzasche hinzu. Die Masse wird gut durchgemischt und noch soviel Wasser zugefügt, daß die verwendete Gesamtwassermenge die Kalkmenge um das vierfache übersteigt.
Die Masse wird in Formen gegossen, wo sie bald aushärtet.
- Vulkanische Bausteine nach Schröder
Sogenannte vulkanische Bausteine werden aus Steinkohlenschlacke und -asche unter Hinzufügung von hydraulischem Kalk und anderen Bindemitteln hergestellt.
Schröder verwendet auf 100 Teile Kohlenasche oder Kohlenschlacke 16 Teile hydraulischen Kalk und 1 Teil Portlandzement. Diese Masse wird gemahlen, gut durchgemischt und dann in Formen gepreßt.
Der Vorteil dieses Verfahrens besteht in der vorteilhaften Verwendung unnützer Abprodukte, deren ständig wachsende Mengen oft belastend sind, in der bedeutenden Festigkeit dieser Steine bei relativer Leichtigkeit, in der großen Widerstandsfähigkeit gegen atmosphärische Einflüsse und der kostengünstigen Herstellung. Aus diesen vulkanischen Bausteinen sind in Deutschland viele massive Wohnhäuser und Gewölbe-Gebäude erbaut.
- Steinmasse nach Mayer
Zuerst werden 5 Teile gelöschter Kalk mit 5 Teilen vorab stark erhitztem Kalk gemischt. 1 Teil dieses Gemischs wird mit 1 Teil Kreide, 2 Teilen Sand, 2 Teilen Quarz- oder Glaspulver und 6 Teilen zu Pulver zerstoßenem Flußspat vermischt, und es wird soviel flüssiges Kalium-Glas (1/3 des spezifischen Gewichtes) hinzugefügt, daß sich eine dünnflüssige Masse ergibt, die sich leicht in Formen gießen läßt und innerhalb von 10 – 40 Min fest wird.
Nach dem Durchtrocknen an der Luft werden die gegossenen Gegenstände abwechselnd mit verdünntem Wasserglas und Silizium-Fluor-Wasserstoff-Säure getränkt.
Auf ähnliche Weise kann man ein Gemisch aus zu gleichen Teilen Glaspulver und Flußspat in konzentriertem Wasserglas bearbeiten.
Für farbige Massen empfiehlt Mayer ein Gemisch ais 2 Teilen Flußspat, 1 Teil Quarz oder Glas und 1 Teil Farbe, die in konzentrierter Wasserglas-Lösung eingerührt ist.
- Steinmassen nach Steyner
Man nimmt feinen Quarzsand und ergänzt, je nach gewünschter Härtestufe, zwischen 2 – 10 % feingemahlenen Bleioxyds. Je fester die Steine sein sollen, desto mehr Bleioxyd ist zuzusetzen. Damit eine farbige Steinmasse entsteht, wird je nach gewünschter Farbe das entsprechende feingemahlene Metalloxyd hinzugefügt.
Das ganze Gemisch wird dann durchgesiebt, damit es sich gut vermischt. Dann wird das Gemisch mit Natrium- oder Kalium-Wasserglas befeuchtet, erneut gut durchgemischt und fest in Formen gepreßt oder gestampft und dann bei mäßiger Temperatur getrocknet.
Nach dem Durchtrocknen wird das Gemisch gebrannt – je nach dem Härtegrad, den man dem herzustellenden Gegenstand geben will, mit mehr oder wenige starker Hitze.
Es ist auch zu bemerken, daß das Wasserglas nicht durch schwefelsaures Natrium verunreinigt sein darf, sonst wird der Stein beim Trocknen bereits zerfallen.
- Steinmasse nach Höfer/Hefer
Für diese ist ein recht weiches Gemisch aus Zementkalk mit Kalium-Wasserglas geeignet, zu dem ein wenig Flußsand hinzugefügt wird. Die Proportion des Zementkalks zum Flußsand ist 2:1.
Bei Verwendung dieser Zementmasse für das Ausbessern von Steintreppen ist es nicht erforderlich, die abgetretenen Stufen herauszuschlagen. Die beschädigten Stellen werden mit Wasserglas bestrichen und darauf wird die frisch zubereitete Masse aufgebracht, der man die erforderliche Form der Stufen gibt. Die Masse härtet im Verlaufe von 6 Stunden aus und wird hart wie Kalkstein.
- Steinmasse nach Schulte
4 – 6 Teile Sand werden mit 1 Teil hydraulischem Kalk vermischt und zum Gemisch werden 6% trockenes möglichst fein zu Pulver zerstoßenes Wasserglas hinzugefügt. Dann wird nochmals als gut durchgemischt und mit einer solchen Menge an Wasser befeuchtet, daß man aus dieser Masse die Steine der gewünschten Form formen kann. Dazu sind etwa 10% Wasser erforderlich.
Die aus dieser Masse gefertigtenSteine läßt man fest werden, wofür etwa 1 – 4 Tage erforderlich sind, danach werden die in einen Bottich mit Wasser gelegt. Unter dem Druck des Wassers löst sich das gleichmäßig in der ganzen Masse v erteilte Wasserglaspulver auf und verbindet sich mit dem Kalk, der ebenfalls in geringem Maße durch das Wasser gelöst wird, zu Silizium-Kalzium-Salz. Wenn nach einige Tagen das Wasserglas sich aufgelöst hat und eine äquivalente Menge Kalk in unlösliches Silizium-Kalzium-Salz verwandelt hat, werden die Steine in Wasser gelegt, welches eine 5%ige Lösung von kohlensaurem Natrium enthält.
Dadurch wird der Rest an freiem Kalk in kohlensauren Kalk verwandelt, während sich das Hydrat des Natriumoxyds löst und durch sorgfältiges Abwaschen in Wasser der bereits festgewordenen Steine entfernt wird. Dann werden die Steine an der Luft getrocknet.
Bei der Verwendung dieses Verfahrens ist eine wesentliche Bedingung, daß das Wasserglas in ungelöstem Zustand als Pulver vorliegt, und daß erst dann die Steine mit einer Lösung von kohlensaurem Natrium bearbeitet werden, wenn alles Wasserglas in Lösung gegangen ist und mit dem Kalk das Silizium-Kalzium-Salz bildet.
- Steinmasse nach Highton
Dieses Verfahren, das in der «Victoria Stone Company» in London verwendet wird, besteht darin, daß kleine Bruchstücke von Granit mit hydaulischem Zement vermischt werden und dann, nach dem Formen und Härten, die Masse in eine Wasserglas-Lösung getaucht wird. Die Granit-Bruchstücke werden zerkleinert und auf jeweils 4 Teile Granit wird 1 Teil Portlandzement beigemengt und das Ganze mit Wasser zu einem Teig vermischt.
Diese Masse wird in Formen gegossen, bleibt 4 Tage stehen und wird dann im Verlaufe von 2 Tagen mit einer 25%igen Lösung siliziumsauren Natriums begossen. Die auf diese Weise hergestellten künstlichen Steine werden hauptsächlich als Bausteine vewendet, als Platten für Stufen und Gehsteige.
- Steinmasse nach Dumenil
1 100 Teile Gips, 10 Teile hydraulischer Kalk, 5 Teile Gelatine und 500 Teile Wasser. Der Gips und der hydraulische Kalk werden in einem Gefäß mit der Gelatine und dem Wasser verrührt, gut durchgemischt und die homogene Masse wird in zerlegbare Holzformen gegossen, die vorher mit grauer Seife eingeschmiert wurden. Nach 20 – 22 Minuten weden die Steine aus den Formen genommen und in der Luft getrocknet, wofür 14 Tage nötig sind.
Je nach Wunsch kann das Durchtrocknen mit künstlicher Wärme beschleunigt werden. Die Steine können in beliebigen Farben durch Hinzufügen von Farbstoffen in die Masse gefärbt werden.
Diese künstlichen Steine können für verschieden Bauarbeiten verwendet werden – für Wohnhäuser, Brücken, Wasserleitungen usw. Die aus dieser Masse gegossenen Steine haben die gleiche Festigkeit wie natürliche Steine und, was besonders wichtig ist, die aus solchen Steinen gebauten Wände leiden nicht unter Feuchtigkeit.
Es versteht sich von selbst, daß man die Steine in beliebigen Formen gießen kann, und auf diese Weise können die verschiedenartigsten Architektur-Details hergestellt werden.
- Steinmasse nach Lebrain
Dieses Verfahren besteht darin, daß hydraulischer Kalk zu feinem Pulver verwandelt wird, das mit Holzkohlepulver (3 – 4 Teile hydraulischer Kalk auf 1 Teil Kohlepulver) vermischt wird. Das Gemisch wird mit Wasser zu einem Teig eingerührt und aus diesem werden Ziegel geformt, die im Kalkbrennofen gebrannt werden.
Nach dem Brennen wird die Masse erneut in feines Pulver verwandelt und dieses Pulver, das Lebrain Hydro nennt, ist der Hauptbestandteil seines Fabrikats.
Die von ihm hergestellten Steine gibt es in zwei Sorten. Eine Sorte besteht aus einem Gemisch von Hydro mit Sand im Verhältnis 1:3 und dient zur Herstellung von Architektur-Ornamenten – Säulen, Kronsteine, Parapets usw.
Die zweite Sorte besteht nur aus dem festgestampften Hydro und dient für Gehwegplatten usw.
Die Masse wird in Eisenformen unter Zusatz von soviel Wasser geformt wie die Former für das Befeuchten von Sand verwenden.
Es ist nachgewiesen, daß die aus dieser Masse gefertigten Gegenstände ihre richtige Form behalten, Reibung und Druck widerstehen und unempfindlich sind gegen atmosphärische Einflüsse.
V. Steinmassen für verschieden Zwecke
- Steinmassen für Filter nach Petri
Für die Herstellung einer porösen Masse, die für Filter, Gefäße u.ä. geeignet ist, nimmt man getrockneten Quarzsand und mischt ihn mit zu Pulver verwandeltem Schwefel (1 Teil auf 4 Teile Sand). Das Gemisch wird in einem flachen Kessel erhitzt, unter ständigem Umrühren, fast bis zum Entflammen des Schwefels. Wenn die Masse den Charakter von feuchtem Sand erreicht, wird sie in einen daneben befindlichen flachen Kessel übertragen, der nicht ganz so stark, aber ebenfalls erhitzt ist, um den Schwefel in der durch das Erhitzen erhaltenen Weichheit und der braunen Farbe zu behalten.
In diesem Kessel wird das Gemisch noch feiner gerührt und dann in die Form gebracht, dessen Aussehen es dann annehmen soll, schnell dort hineingedrückt und sofort mit kalten Wasser übergossen, welches durch die poröse Masse dringt und durch im Boden der Form befindliche Öffnungen abfließt.
Es ist anfangs nicht zuviel Wasser draufzugießen, damit in der Masse nicht zuviel Dampf entsteht. Anstelle de Abkühlung mit Wasser kann in bekannten Fällen die Form unten auch mit einen Zusatz versehen werden, in welchen der überflüssige Schwefel abgegossen wird. Der Gegenstand hat dann genauso einen Zusatz, der dann abgeschnitten wird.
Anstelle von nur Schwefel kann auch ein Gemisch von Schwefel mit Ton verwendet werden. Für einige Zwecke empfiehlt es sich, zur Masse eine gewisse Menge (1 – 10%) Harz, Pech, Guttapercha usw. zuzusetzen. Dieser oder anderer Stoff wird erst gut bei Wärme mit dem Sand vermischt und dann wird der Schwefel zugegeben.
Wenn man eine wasserundurchlässige Masse erhalten will, die auch starken Säuren widersteht, so wird als Material, mit dem der Schwefel vermischt wird, feiner oder grober Sand oder Schotter genommen und dem werden noch größere Kiesel zugefügt, deren Dicke jedoch 1/8 der Wandstärke des herzustellenden Gegenstandes nicht übersteigen darf.
Diese Masse wird in der Wärme mit einer solche Menge an reinem Schwefel oder gemischtem mit Ton (oder je nach Umständen mit Harz) vermischt, daß der Schwefel alle Zwischenräume zwischen den Teilchen der Masse ausfüllt; wenn der Schwefel den in höchstem Maße flüssigen Zustand erreicht, wird die Masse in die Form gelegt.
Aus dieser Masse wird empfohlen, ebenfalls Gefäße und Rohre für chemische Zwecke herzustellen.
- Steinmasse für Schleifsteine
Die Ingenieure Keppel und Kübler aus Stuttgart empfehlen folgenes unkompliziertes Verfahren für die Herstellung von guten Schleifsteinen: 2 Teile Portlandzement und 1 Teil feingemahlener Quarz werden mit Wasser bis zum Erhalt einer dünnflüssigen Masse verrührt, danach in entsprechende Formen mit den geforderten Abmessungen vergossen und im Verlaufe von 12 Tagen getrocknet.
Wenn die nach diesem Verfahren hergestellte Masse ausgetrocknet ist, wird sie aus der Form genommen und für einige Zeit in eine Lösung aus gleichen Teilen von schwefelsaurem Kupfer und schwefelsaurem Zink gelegt; in dieser Lösung werden alle Poren der geformten Masse gefüllt und der Stein erhält die Eigenschaften des besten natürlichen Schleif- oder Poliersteins.
- Künstliche lithografische Steine
Die Masse besteht aus Portlandzement, Sand, gelöschtem Kalk und Ton. Der Portlandzement hat selbst schon annähernd die Zusammensetzung, die für einen lithografischen Stein gefordert ist – er enthält Kalk und Tonerde.
Das Buch „Handbuch des Handwerkers“ ( in russisch) herunterladen
Wie wir sehen, war das Gießen von künstlichen Steinen nicht nur die Spielweise geheimer Labors in jesuitischen Klöstern.
In der Sowjetunion wurden wissende Fachleute hoch geschätzt und es kam niemandem in den Sinn, irgendetwas vor den Volk zu verbergen. Mit Ausnahme jener Fragen, welche die Politik betrafen – versteht sich – und potentielle Gefahren für die Gesellschaft.
Aber ich habe noch Zeiten erlebt, als in ganz Moskau viereckige Müllbehälter aus rotem poliertem Granit standen.
Etwa solche:
Und sie waren monolithisch, hatten keine Nähte, was unmöglich gewesen wäre beim Versuch, diese Gegenstände aus natürlichem Stein durch Sägen herzustellen.
Deshalb kann man sagen, daß rudimentäre Kenntnisse über das, was heute vom Schweizer Josef Dawidowitz patentiert ist, wie Geo-Polimer-Beton, nicht von ihm erfunden wurde, und auch nicht von sowjetischen Gelehrten.
Diese Techologien waren in breiter Anwendung beim Bau von vielen in der ganzen Welt bekannten Kunstwerken der Architektur des 18. und 19. Jahrhunderts.
Es folgen Fotos einiger leuchtender Illustrationen dessen, die mir aus der Grande Opera (Paris, Frankreich) zugesandt wurden. Autorin der Fotos ist Christine Fet:
Es wir sich kaum ein geistig gesunder Mensch finden, der den Worten des Fremdenführers glaubt, daß dies aus natürlichem Marmor herausarbeitet ist, mit Hilfe von Hammer und Meißel.
Es ist völlig offensichtlich, da die Geländerpfosten/Balustersäulen mit dem Verfahren des Formgießens hergestellt wurden, aus der gleichen Form. Sind sind absolut identisch, mit Ausnahme der Textur.
Na, und hier sind wohl Kommentare überflüssig. Ein Abguß der Büste des Montferrand in der Isaaks-Kathedrale (in Sankt Petersburg):
Wenn diese Faletti mit seinen Handwerkzeugen geschaffen hat… dann soll doch jemand mal auf diese Weise etwas auch nur annähernd ähnliches erschaffen! Wird keiner können.
Und die Säulen mit gigantischen Ausmaßen macht keiner aus Malachit. Und die Vase aus einem „monolithischen Stück Malachit“, die in der Ermitage steht, kann auch niemand nachmachen. Warum wohl?
Es ist offensichtlich, daß es in der Natur keine Stücke homogener Mineralien solch riesiger Ausmaße gibt. An das Märchen darüber, daß man diese alle schon gefunden und benutzt hat und nun nur noch kleine Steinchen übrig sind, glaubt doch kaum noch einer.
Wenn es sowas gäbe, dann würde man auch heutzutage noch sowas finden.
Aber es hat noch keiner Goldklumpen von der Größe eine Autobusses gefunden, und niemand hat je monolithische Riesenblöcke aus Lasurit oder Malachit gesehen, aus denen man eine ganze Säule von 5 – 6 Metern Höhe herausdrehen könnte.
Das ist alles so hergestellt, wie in jenem Handbuch des Handwerkers. Oder ganz ähnlich.
Und schaut mal, was für Artefakte im Louvre lagern (Autorin der Fotos: Christine Fet):
Nicht ein Firma, die sich heutzutage mit der Herstellung von Erzeugnissen aus Natursteinen befaßt, würde es sich zutrauen, diesen Sarkophag nachzubauen.
Man wird euch sagen, da man etwas ähnliches aus mehren Teilen erschaffen kann.
Aber Werkzeuge, die es ermöglichen aus einem Monolithen einen inneren Hohlraum anzufertigen, mit rechtenwinkligen Ecken, gibt es einfach nicht.
Ich erinnere daran, daß der Sarkopharg aus Diorit hergestellt ist, das eines der härtesten natürlichen Minerale ist. Er ist mit Handwerkzeugen praktisch nicht zu bearbeiten.
All das ist ebenfalls Diorit. Diese Inschriften kann man mit Schlagwerkzeugen unmöglich herausschlagen. Sowas kann man nur durch Eindrücken in weiches Material machen, oder mit Hilfe eines Reliefs an der Innenseite der Form, in welcher der Guß erfolgt ist.
Bitte jetzt keine „Erklärungen“ anbieten, von wegen 3D-Drucker, Laseranlage mit SPS und Außerirdischen.
Es entsteht gesetzmäßig die Frage: sind ägyptische Sarkophage und sonstige „Pfannen“ aus Diorit in Wirklichkeit so uralt wie uns die Gelehrten erzählen, oder sind sie etwa Zeitgenossen jener Artefakte, die sich in der Grande Opera befinden?
Man versucht uns zu überzeugen, daß sie eine Unzahl von Jahrtausenden alt sind, aber ich sehe da Technologien des 18. Jahrhunderts.
Denn es zeigt sich, daß die Mehrzahl dessen, was heute gewissenlos als antik ausgegeben wird, tatsächlich erst Ende des 19. – Anfang des 20. Jahrhunderts erschaffen wurde, auf gigantisch großen Drehbänken mit Dampfmaschinenantrieb und mit Hilfe von mechanischen Werkzeugen, die mit Druckluft-Energie in Gang gebracht wurden.
Quelle der Übersetzung